In an era where technology continues to evolve at an unprecedented rate, one innovation stands out as a harbinger of a manufacturing renaissance: 3D printing. Often hailed as the future of production, 3D printing, or additive manufacturing, transcends the limitations of traditional methods, transforming digital visions into tangible realities.
At its core, it’s a process that meticulously crafts three-dimensional objects layer by layer, juxtaposing creativity with precision. With an array of methodologies under its umbrella, each tailored to distinct applications and materials, 3D printing is not just a singular technique but a symphony of processes harmonizing the future of design and fabrication.
What is 3D Printing Technology?
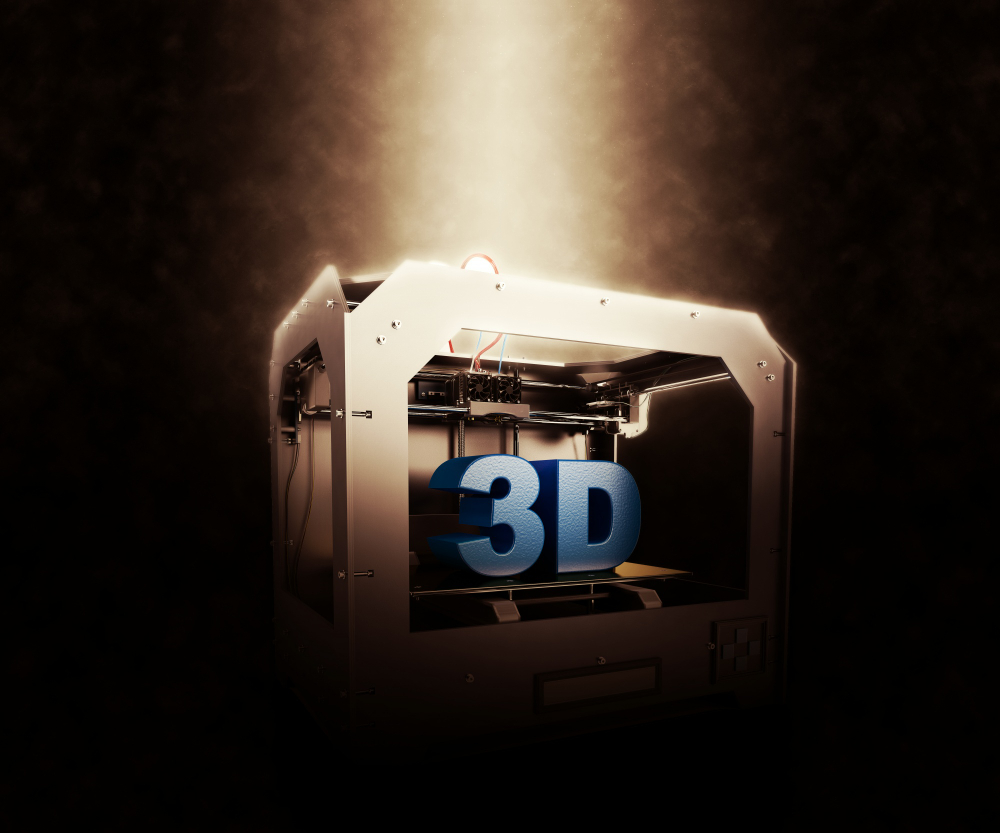
3D printing, frequently referred to as additive manufacturing, represents a groundbreaking approach to object creation. Originating from a digital blueprint or file, this method fabricates tangible, three-dimensional items by systematically adding material layer upon layer.
This additive process contrasts starkly with conventional manufacturing techniques that remove material, such as carving or drilling. By focusing solely on adding material where the design necessitates, 3D printing offers an unparalleled level of design versatility and precision. Moreover, this method is inherently efficient, significantly reducing waste as only the necessary amount of material is used, making it both an innovative and environmentally-conscious choice in manufacturing.
How Does 3D Printing Technology Work?

The journey of 3D printing an object typically begins with a digital blueprint. This is usually created using computer-aided design (CAD) software. Once the design is finalized:
1. Digital Blueprint Creation
The conception of any 3D-printed object is rooted in its design. Digital blueprints, pivotal to this process, are crafted using Computer-Aided Design (CAD) software. These sophisticated programs enable designers to envisage and refine their creations in a virtual space, allowing for intricate detailing, precise measurements, and iterative modifications. Once the designer is satisfied, the model stands ready for the next phase.
2. Slicing
Before an object can be realized in the physical realm, its digital representation must undergo a transformation known as ‘slicing’. Here, the 3D model is segmented into ultra-thin horizontal cross-sections. Specialized slicing software undertakes this task, subsequently generating a file that meticulously instructs the 3D printer. Each slice equates to a single layer of the eventually printed object, dictating how it will be constructed step by step.
3. Printing
With instructions in hand, the 3D printer embarks on the monumental task of object fabrication. Interpreting the sliced file, the printer meticulously deposits, cures, or fuses material, layer by fragile layer. The chosen printing technology and material define this method – whether it’s melting plastic filament, curing resin with UV light, or fusing metal powders with a laser. This iterative process continues unabated until the digital design becomes a tangible reality.
4. Post-processing
Birthed from the printer, the object often emerges with imperfections or residual structures that supported it during its creation. The post-processing phase is where these newborn artifacts undergo refinement. This might involve removing these supporting structures, sanding down rough patches, or even applying paint or coatings for aesthetic and functional enhancement. Only after this meticulous grooming does the printed object truly realize its final form, ready for the world.
Different Types of 3D Printing Technologies
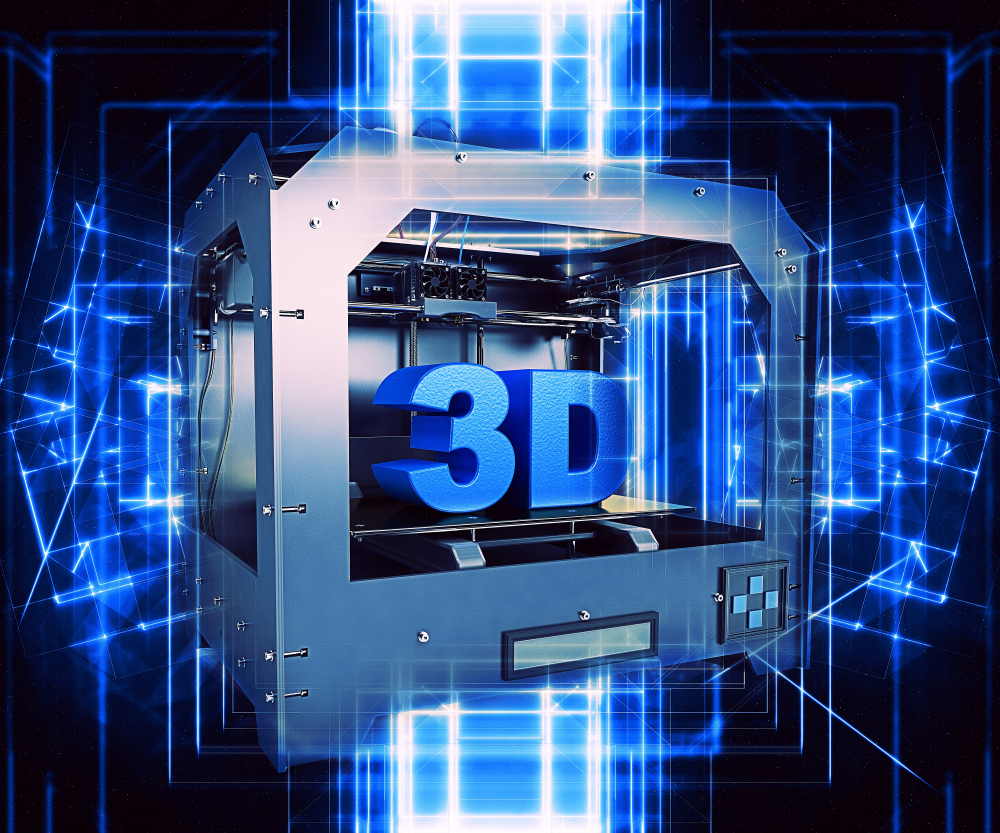
1. Stereolithography (SLA)
Stereolithography (SLA) operates on an intricate interplay of light and chemistry. Central to this process is an ultraviolet (UV) laser, which dances across a vat filled with liquid resin. As the laser makes its journey, it selectively hardens the resin wherever it touches. This curing happens layer by painstaking layer, eventually coalescing into a solid three-dimensional structure. Unlike methods that rely on heat or extrusion, SLA is all about precision photochemical reactions initiated by the UV laser’s energy.
Applications of SLA
Owing to its exceptional precision, SLA is the method of choice for projects demanding intricate details and high fidelity to the original design. Jewelers, for instance, often turn to SLA to achieve the delicate and precise structures of their designs. The medical and dental fields, where precision can be a matter of health, also frequently employ SLA. Detailed anatomical models, dental molds, and even hearing aids have been realized using this technology. Moreover, product designers and engineers utilize SLA for prototypes, enabling them to visualize and test designs before entering large-scale production.
The magic potion in SLA’s process is the photosensitive liquid resin. These resins contain molecules that, when exposed to UV light, undergo a chemical transformation that causes them to solidify. The specific properties of the resin – its color, strength, flexibility, and even transparency – can be varied depending on the intended application of the final object. As research progresses, the variety and capabilities of these resins continue to expand, offering designers and engineers an ever-growing palette of material properties to choose from.
2. Selective Laser Sintering (SLS)
The realm of Selective Laser Sintering (SLS) revolves around the power of finely tuned laser energy. In this process, a high-powered laser meticulously fuses minute particles of powder, be it polymer or metal, layer by layer. As the laser scans the powder bed based on the digital blueprint, targeted regions are sintered while others remain unaffected. Once a layer is completely sintered, the platform descends, a new layer of powder is spread, and the process repeats, ultimately yielding a solid structure embedded within the unused powder.
Applications Of SLS
SLS stands out for its ability to produce robust and complex geometries without the need for supporting structures, a trait that makes it particularly attractive for intricate designs. This technology finds its utility in a range of sectors. From aerospace components that benefit from the weight-saving opportunities of intricate lattice structures to fashion accessories that flaunt avant-garde designs, SLS has made a mark. Moreover, it’s a favored choice for rapid prototyping, where designers can quickly iterate and test functional parts due to the durability of SLS-produced items.
The versatility of SLS is also manifested in its material palette. While the most common material is nylon or its variants, a gamut of polymers, ceramics, and even some metals can be employed. Depending on the chosen material, the properties of the finished object—strength, flexibility, heat resistance, and more—can be tailored. Researchers and manufacturers continuously explore new powder formulations to expand the horizons of what SLS can achieve, further cementing its position as a versatile and valuable additive manufacturing technique.
3. Fused Deposition Modeling (FDM)
Fused Deposition Modeling (FDM), one of the most widely recognized 3D printing techniques, functions by extruding a thermoplastic filament through a heated nozzle. As this melted filament is precisely deposited onto the build platform, it cools and solidifies, establishing the foundation for the object. The printer’s print head navigates in specific patterns dictated by the digital model, constructing the object layer by layer. With each subsequent layer, the filament bonds with the preceding one, steadily building upwards until the entire model is realized.
Applications Of FDM
FDM’s relative ease of use and cost-effectiveness have made it a favorite among hobbyists, educators, and professionals alike. Its applications span from the creation of simple household items, toys, and tooling components to more complex prototypes and even some end-use parts. Given its adaptability, FDM serves as an ideal solution for rapid prototyping, allowing engineers and designers to swiftly turn their digital ideas into tangible prototypes for testing and refinement.
The material breadth for FDM is expansive, driven by the myriad of available thermoplastic filaments. From the commonly used Acrylonitrile Butadiene Styrene (ABS) and Polylactic Acid (PLA) to more specialized materials like thermoplastic elastomers, polyethylene terephthalate glycol (PETG), and high-temperature resistant polycarbonates, the options are vast. Each material brings its own set of characteristics to the table, such as flexibility, strength, transparency, or resistance to various environmental conditions, allowing users to select the optimal filament for their specific project needs.
4. Digital Light Process (DLP)
Digital Light Process (DLP) bears a semblance to SLA in its core methodology but introduces its unique flair. At its heart, DLP utilizes a digital light projector screen to flash an entire layer of the object’s image onto the surface of a UV-sensitive liquid resin. Instead of tracing paths with a UV laser, DLP projects the full image of the layer, hardening the resin wherever the light hits. This simultaneous curing of an entire layer can often lead to faster print times compared to other methods that build layer by layer.
Applications Of DLP
The rapidity and precision of DLP make it a favored choice for industries where detail and speed converge. It’s extensively used in the dental and medical sectors for creating intricate structures like dental crowns or hearing aids. Additionally, jewelers appreciate the crisp details DLP can capture, essential for intricate designs. In the realms of entertainment and prototyping, DLP finds its niche in creating finely detailed miniatures and models, bringing fantastical concepts to tangible life.
DLP operates using photopolymers, which are UV-sensitive resins that solidify upon exposure to specific light wavelengths. These resins can be fine-tuned for a range of properties, including rigidity, flexibility, transparency, and even color. Advancements in material science have birthed resins that mimic certain ceramics or metals, expanding the applications of DLP even further. The continued evolution of these materials, paired with DLP’s inherent precision, promises even more innovation in the near future.
5. Multi Jet Fusion (MJF)
Multi Jet Fusion (MJF) is a revolutionary 3D printing technique that redefines the boundaries of speed and precision. Unlike traditional layer-by-layer additive methods, MJF employs a multi-step process. First, a thin layer of powder material is laid on the build platform. Subsequently, inkjet array heads sweep across, depositing fusing and detailing agents in specific patterns. These agents denote which areas will be sintered and which will remain unaltered. A powerful heating element then passes over the bed, causing areas with the fusing agent to melt and bond, while the detailing agent helps define finer features and edges. The process repeats, building the object layer by layer.
Applications Of Multi-Jet Fusion
Owing to its impressive speed and ability to create intricate, durable parts, MJF finds robust applications across industries. From aerospace to automotive sectors, the technique is employed to produce functional prototypes and even some final parts, prized for their durability and detail. Furthermore, the medical industry leverages MJF for patient-specific implants and surgical tools, benefiting from the technology’s precision and customization capabilities.
MJF primarily uses nylon-based powders, renowned for their strength and flexibility. However, as the technology matures, an expanding array of materials is being introduced, ranging from different polyamides to elastomers. This growing materials palette ensures that parts produced via MJF can be tailored to meet specific requirements, whether it’s rigidity, heat resistance, or flexibility. Researchers are continuously pushing the envelope, exploring new materials that can further elevate the potential of MJF.
6. PolyJet Technology
PolyJet is a sophisticated 3D printing method that mirrors the principles of inkjet printing but goes a step further by crafting three-dimensional objects. Utilizing a print head, the technology jets out minuscule droplets of liquid photopolymer onto the build tray, shaping the design layer by layer. Immediately after deposition, each droplet is cured (or solidified) by UV light. One of PolyJet’s standout features is its ability to print multiple materials simultaneously, allowing for multi-color and multi-material objects with varying properties within a single print.
Applications Of PloyJet Technology
Due to its high resolution and capacity for intricate detailing, PolyJet is a favored choice in industries where precision and aesthetics converge. The automotive and consumer goods sectors employ PolyJet for detailed prototypes, enabling designers to visualize products with realism unparalleled by other techniques. Medical professionals use it to create detailed anatomical models, while researchers benefit from its ability to create complex geometries for academic studies. Furthermore, the versatility of PolyJet shines in creating molds, patterns, and even some end-use parts that demand intricate detailing and varying material properties.
PolyJet’s material spectrum is vast and versatile, from rigid to flexible, transparent to opaque, and neutral to vibrantly colored. These photopolymers can mimic various properties, from the elasticity of rubber to the hardness of ABS. A distinguishing feature is the technology’s capability to blend multiple resins during printing, producing what’s known as ‘Digital Materials’. This blending facilitates the creation of objects with gradient properties — for example, a prototype with both rigid and soft regions, or a model that transitions smoothly from one color to another.
7. Direct Metal Laser Sintering (DMLS)
Direct Metal Laser Sintering (DMLS) stands at the frontier of metal 3D printing techniques, offering unparalleled precision and material strength. At its core, DMLS utilizes a high-powered laser to selectively fuse metal powder particles, building an object layer by layer. As the laser scans each layer based on the digital blueprint, it melts the powder in specific areas to form a solid structure. Once a layer is sintered, the build platform descends, and a new layer of metal powder is spread, ready for the subsequent pass of the laser.
Applications Of DMLS
DMLS’s ability to craft durable metal components with intricate geometries has cemented its position in sectors demanding high performance and precision. Aerospace and automotive industries employ DMLS for producing parts that are both lightweight and robust. Medical professionals and researchers adopt DMLS to create custom implants and surgical instruments, leveraging the technology’s ability to tailor designs to individual patient needs. Moreover, tooling and manufacturing sectors harness DMLS for creating molds and dies with complex cooling channels, optimizing their processes.
The material arsenal for DMLS predominantly comprises metals and metal alloys. Commonly used metals include stainless steel, aluminum, titanium, and cobalt-chrome. Each material offers unique properties ranging from corrosion resistance to high strength-to-weight ratios. The broad material palette ensures that DMLS-produced parts can be finely tuned to meet specific industry standards and performance criteria. As research progresses, more metals and alloys are continually being evaluated and added to the DMLS repertoire, further expanding its potential.
8. Electron Beam Melting (EBM)
Electron Beam Melting (EBM) is an advanced 3D printing technique that, like DMLS, is tailored for metal components. Instead of a laser, however, EBM employs a powerful electron beam to melt and fuse metal powder particles. Operating within a vacuum and at high temperatures, the electron beam scans over the powder bed, melting specific regions based on the digital blueprint. Once a layer is fully melted, the build platform descends, and a new layer of metal powder is spread out, readying it for the next pass of the electron beam.
Applications Of EBM
EBM’s hallmark is its ability to produce dense and strong metal parts, often with superior mechanical properties compared to other methods. This has made it invaluable in industries like aerospace, where the strength-to-weight ratio is paramount. Additionally, the medical sector has embraced EBM for crafting orthopedic implants, benefiting from the technique’s capability to create porous structures that promote bone integration. The high melting point achieved by EBM also ensures components have excellent thermal resistance, opening avenues for its application in high-temperature environments like jet engines.
Materials for EBM are centered around metals that can withstand high temperatures within the EBM chamber. Titanium and its alloys are particularly popular due to their favorable properties, such as biocompatibility and strength. Cobalt-chrome and nickel-based superalloys also feature prominently, chosen for their thermal resistance and mechanical strength. As the technique continues to mature, research is underway to expand the list of compatible metals and alloys, broadening the horizons of EBM applications.
Conclusion
The domain of 3D printing is akin to an expansive tapestry, intricately woven with threads of innovation, precision, and versatility. From crafting intricate jewelry through SLA to forging robust aerospace components with EBM, the spectrum of possibilities seems boundless.
As industries across the globe increasingly embrace these technologies, we stand on the precipice of a new industrial age, one where design intricacies are no longer fettered by production constraints. Indeed, as we delve deeper into the intricacies of each 3D printing method, it becomes evident that we’re not just shaping materials but the very future of manufacturing itself.
